A tecnoloxía de corte en dados de obleas, como paso fundamental no proceso de fabricación de semicondutores, está directamente ligada ao rendemento, o rendemento e os custos de produción do chip.
#01 Antecedentes e importancia do corte en obleas
1.1 Definición de corte en dados de obleas
O corte en dados de obleas (tamén coñecido como gravado) é un paso esencial na fabricación de semicondutores, destinado a dividir as obleas procesadas en varios chips individuais. Estes chips adoitan conter funcionalidades de circuíto completas e son os compoñentes principais que se usan en última instancia na produción de dispositivos electrónicos. A medida que os deseños de chips se volven máis complexos e as dimensións seguen reducindo, os requisitos de precisión e eficiencia para a tecnoloxía de corte en dados de obleas son cada vez máis estritos.
Nas operacións prácticas, o corte en dados de obleas adoita empregar ferramentas de alta precisión, como láminas de diamante, para garantir que cada dado permaneza intacto e totalmente funcional. Os pasos clave inclúen a preparación antes do corte, un control preciso durante o proceso de corte e a inspección de calidade despois do corte.
Antes de cortar, a oblea debe marcarse e colocarse para garantir traxectorias de corte precisas. Durante o corte, os parámetros como a presión e a velocidade da ferramenta deben controlarse estritamente para evitar danos na oblea. Despois do corte, realízanse inspeccións de calidade exhaustivas para garantir que cada chip cumpra os estándares de rendemento.
Os principios fundamentais da tecnoloxía de corte en dados de obleas abarcan non só a selección do equipo de corte e o axuste dos parámetros do proceso, senón tamén a influencia das propiedades mecánicas e características dos materiais na calidade do corte. Por exemplo, as obleas de silicio dieléctrico de baixa k, debido ás súas propiedades mecánicas inferiores, son moi susceptibles á concentración de tensión durante o corte, o que leva a fallos como lascado e rachaduras. A baixa dureza e fraxilidade dos materiais de baixa k fanos máis propensos a danos estruturais baixo forza mecánica ou tensión térmica, especialmente durante o corte. O contacto entre a ferramenta e a superficie da oblea, xunto coas altas temperaturas, pode exacerbar aínda máis a concentración de tensión.
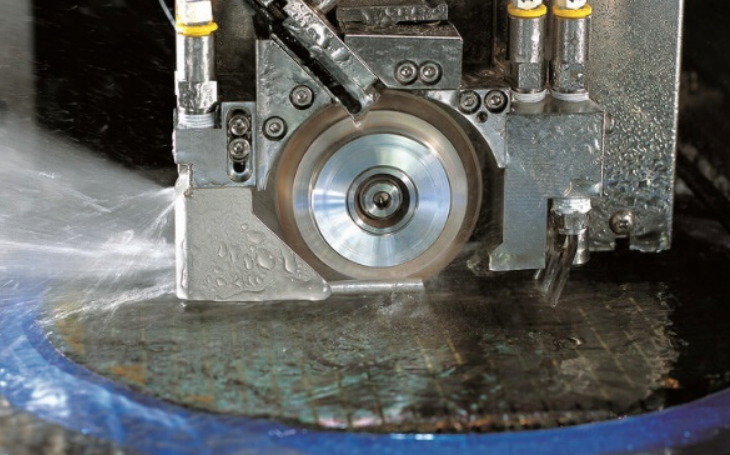
Cos avances na ciencia dos materiais, a tecnoloxía de corte en dados de obleas expandiuse máis alá dos semicondutores tradicionais baseados en silicio para incluír novos materiais como o nitruro de galio (GaN). Estes novos materiais, debido á súa dureza e propiedades estruturais, supoñen novos desafíos para os procesos de corte en dados, o que require novas melloras nas ferramentas e técnicas de corte.
Como proceso crítico na industria dos semicondutores, o corte en dados de obleas continúa a optimizarse en resposta ás demandas en evolución e aos avances tecnolóxicos, sentando as bases para as futuras tecnoloxías de microelectrónica e circuítos integrados.
As melloras na tecnoloxía de corte en obleas van máis alá do desenvolvemento de materiais e ferramentas auxiliares. Tamén abarcan a optimización de procesos, melloras no rendemento dos equipos e un control preciso dos parámetros de corte. Estes avances teñen como obxectivo garantir unha alta precisión, eficiencia e estabilidade no proceso de corte en obleas, satisfacendo a necesidade da industria dos semicondutores de dimensións máis pequenas, maior integración e estruturas de chips máis complexas.
Área de Mellora | Medidas específicas | Efectos |
Optimización de procesos | - Mellorar os preparativos iniciais, como un posicionamento máis preciso das obleas e unha planificación de rutas. | - Reducir erros de corte e mellorar a estabilidade. |
- Minimizar os erros de corte e mellorar a estabilidade. | - Adoptar mecanismos de monitorización e retroalimentación en tempo real para axustar a presión, a velocidade e a temperatura da ferramenta. | |
- Reducir as taxas de rotura das obleas e mellorar a calidade do chip. | ||
Mellora do rendemento do equipo | - Utilizar sistemas mecánicos de alta precisión e tecnoloxía avanzada de control automatizado. | - Mellorar a precisión do corte e reducir o desperdicio de material. |
- Introducir tecnoloxía de corte por láser axeitada para obleas de materiais de alta dureza. | - Mellorar a eficiencia da produción e reducir os erros manuais. | |
- Aumentar a automatización dos equipos para a monitorización e os axustes automáticos. | ||
Control preciso de parámetros | - Axusta con precisión parámetros como a profundidade de corte, a velocidade, o tipo de ferramenta e os métodos de arrefriamento. | - Garantir a integridade da matriz e o rendemento eléctrico. |
- Personaliza os parámetros en función do material, o grosor e a estrutura da oblea. | - Aumentar as taxas de rendemento, reducir o desperdicio de materiais e diminuír os custos de produción. | |
Importancia estratéxica | - Explorar continuamente novas vías tecnolóxicas, optimizar procesos e mellorar as capacidades dos equipos para satisfacer as demandas do mercado. | - Mellorar o rendemento e a fabricación de chips, apoiando o desenvolvemento de novos materiais e deseños avanzados de chips. |
1.2 A importancia do corte en dados de obleas
O corte en dados das obleas xoga un papel fundamental no proceso de fabricación de semicondutores, o que inflúe directamente nos pasos posteriores, así como na calidade e o rendemento do produto final. A súa importancia pódese detallar do seguinte xeito:
En primeiro lugar, a precisión e a consistencia do corte en dados son fundamentais para garantir o rendemento e a fiabilidade do chip. Durante a fabricación, as obleas sofren múltiples pasos de procesamento para formar numerosas estruturas de circuítos complexas, que deben dividirse con precisión en chips individuais (die). Se hai erros significativos na aliñación ou no corte durante o proceso de corte en dados, os circuítos poden danarse, o que afecta á funcionalidade e á fiabilidade do chip. Polo tanto, a tecnoloxía de corte en dados de alta precisión non só garante a integridade de cada chip, senón que tamén evita danos nos circuítos internos, mellorando a taxa de rendemento xeral.
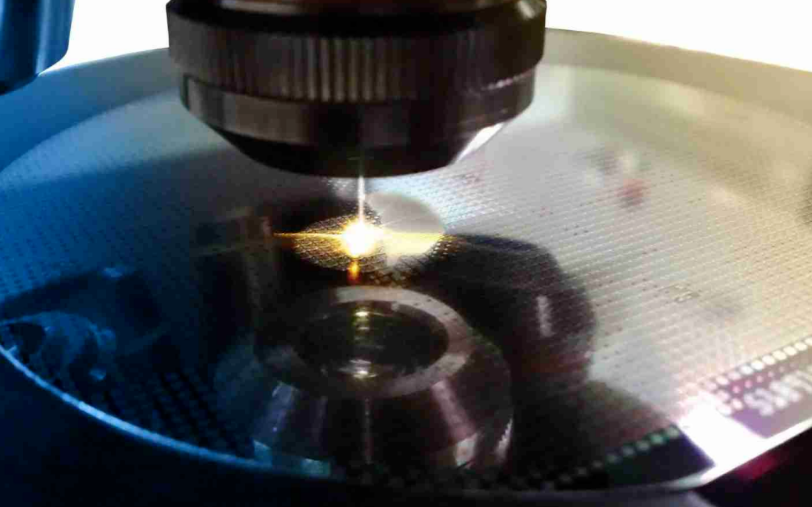
En segundo lugar, o corte en dados de obleas ten un impacto significativo na eficiencia da produción e no control de custos. Como paso crucial no proceso de fabricación, a súa eficiencia afecta directamente ao progreso dos pasos posteriores. Ao optimizar o proceso de corte en dados, aumentar os niveis de automatización e mellorar as velocidades de corte, a eficiencia xeral da produción pode mellorar considerablemente.
Por outra banda, o desperdicio de material durante o corte en dados é un factor crítico na xestión de custos. A utilización de tecnoloxías avanzadas de corte en dados non só reduce as perdas innecesarias de material durante o proceso de corte, senón que tamén aumenta a utilización das obleas, o que reduce os custos de produción.
Cos avances na tecnoloxía dos semicondutores, os diámetros das obleas seguen a aumentar e, en consecuencia, as densidades dos circuítos aumentan, o que supón unha maior demanda de tecnoloxía de corte en dados. As obleas máis grandes requiren un control máis preciso das rutas de corte, especialmente en áreas de circuítos de alta densidade, onde mesmo pequenas desviacións poden facer que varios chips sexan defectuosos. Ademais, as obleas máis grandes implican máis liñas de corte e pasos de proceso máis complexos, o que require novas melloras na precisión, consistencia e eficiencia das tecnoloxías de corte en dados para afrontar estes desafíos.
1.3 Proceso de corte en dados de obleas
O proceso de corte en dados de obleas abrangue todos os pasos, dende a fase de preparación ata a inspección de calidade final, sendo cada etapa fundamental para garantir a calidade e o rendemento dos chips cortados en dados. A continuación, ofrécese unha explicación detallada de cada fase.
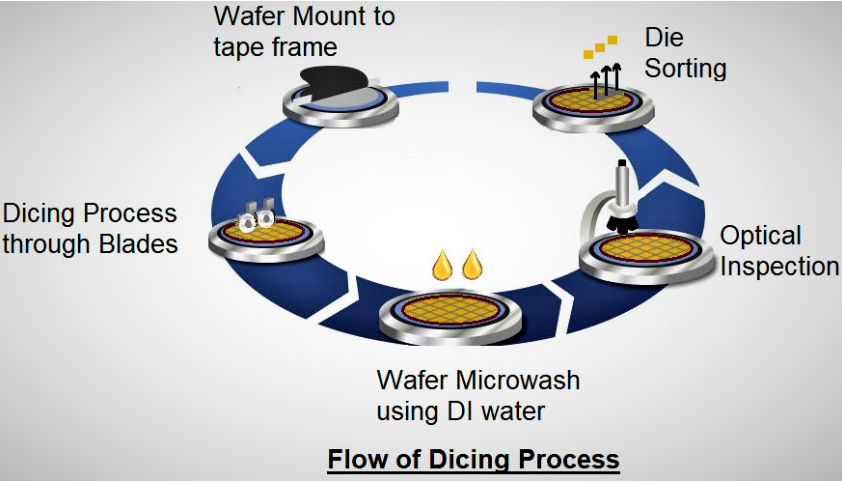
Fase | Descrición detallada |
Fase de preparación | -Limpeza de obleasEmpregar auga de alta pureza e axentes de limpeza especializados, combinados con fregado ultrasónico ou mecánico, para eliminar impurezas, partículas e contaminantes, garantindo unha superficie limpa. -Posicionamento precisoUtilizar equipos de alta precisión para garantir que a oblea se divida con precisión ao longo das traxectorias de corte deseñadas. -Fixación de obleasFixar a oblea nun marco de cinta para manter a estabilidade durante o corte, evitando danos por vibracións ou movemento. |
Fase de corte | -Corte de láminasEmpregan láminas revestidas de diamante rotatorias de alta velocidade para corte físico, axeitadas para materiais a base de silicona e rendibles. -Corte láser en dadosUtilizan raios láser de alta enerxía para cortes sen contacto, ideais para materiais fráxiles ou de alta dureza como o nitruro de galio, o que ofrece unha maior precisión e menos perda de material. -Novas tecnoloxíasIntroducir tecnoloxías de corte por láser e plasma para mellorar aínda máis a eficiencia e a precisión, minimizando ao mesmo tempo as zonas afectadas pola calor. |
Fase de limpeza | - Empregar auga desionizada (auga DI) e axentes de limpeza especializados, combinados con limpeza por ultrasóns ou por pulverización, para eliminar os residuos e o po xerados durante o corte, evitando que os residuos afecten aos procesos posteriores ou ao rendemento eléctrico da lasca. - A auga desionizada de alta pureza evita a introdución de novos contaminantes, garantindo un ambiente de oblea limpo. |
Fase de inspección | -Inspección ópticaEmpregar sistemas de detección óptica combinados con algoritmos de IA para identificar rapidamente defectos, garantindo que non haxa gretas nin lascas nas lascas cortadas en dados, mellorando a eficiencia da inspección e reducindo o erro humano. -Medición de dimensións: Verificar que as dimensións do chip cumpran as especificacións de deseño. -Probas de rendemento eléctricoAsegurar que o rendemento eléctrico dos chips críticos cumpra cos estándares, garantindo a fiabilidade en aplicacións posteriores. |
Fase de clasificación | - Use brazos robóticos ou ventosas de baleiro para separar as fichas cualificadas do marco da cinta e clasificalas automaticamente segundo o rendemento, garantindo a eficiencia e a flexibilidade da produción e mellorando a precisión. |
O proceso de corte de obleas implica a limpeza, o posicionamento, o corte, a limpeza, a inspección e a clasificación das obleas, sendo cada paso crítico. Cos avances na automatización, o corte por láser e as tecnoloxías de inspección por IA, os sistemas modernos de corte de obleas poden lograr unha maior precisión, velocidade e unha menor perda de material. No futuro, as novas tecnoloxías de corte como o láser e o plasma substituirán gradualmente o corte tradicional de láminas para satisfacer as necesidades de deseños de chips cada vez máis complexos, impulsando aínda máis o desenvolvemento de procesos de fabricación de semicondutores.
Tecnoloxía de corte de obleas e os seus principios
A imaxe ilustra tres tecnoloxías comúns de corte de obleas:Corte de láminas,Corte láser en dados, eCorte por plasmaA continuación móstrase unha análise detallada e unha explicación complementaria destas tres técnicas:
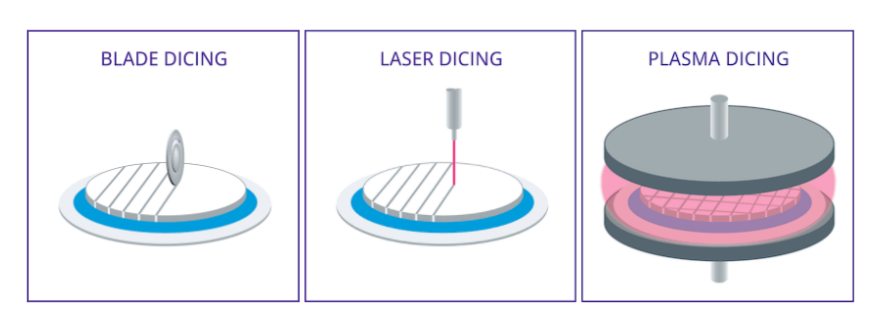
Na fabricación de semicondutores, o corte de obleas é un paso crucial que require seleccionar o método de corte axeitado en función do grosor da oblea. O primeiro paso é determinar o grosor da oblea. Se o grosor da oblea supera as 100 micras, pódese escoller o corte por láminas como método de corte. Se o corte por láminas non é axeitado, pódese usar o método de corte por fractura, que inclúe tanto técnicas de corte por rayado como de corte por láminas.
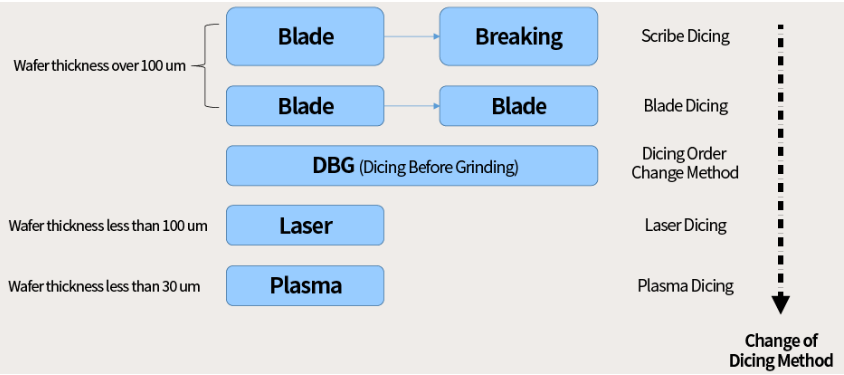
Cando o grosor da oblea está entre 30 e 100 micras, recoméndase o método DBG (Dice Before Grinding, en inglés, en dados antes da moenda). Neste caso, pódese escoller o corte por rayado, o corte con lámina ou o axuste da secuencia de corte segundo sexa necesario para obter os mellores resultados.
Para obleas ultrafinas cun grosor inferior a 30 micras, o corte por láser convértese no método preferido debido á súa capacidade para cortar obleas delgadas con precisión sen causar danos excesivos. Se o corte por láser non pode cumprir requisitos específicos, pódese empregar o corte por plasma como alternativa. Este diagrama de fluxo proporciona unha vía clara para a toma de decisións para garantir que se escolla a tecnoloxía de corte de obleas máis axeitada en diferentes condicións de grosor.
2.1 Tecnoloxía de corte mecánico
A tecnoloxía de corte mecánico é o método tradicional para o corte de obleas. O principio básico é usar unha rebarbadora de diamante rotatoria de alta velocidade como ferramenta de corte para cortar a oblea. O equipo clave inclúe un eixo con soporte de aire, que acciona a ferramenta da rebarbadora de diamante a altas velocidades para realizar cortes ou ranurados precisos ao longo dunha traxectoria de corte predefinida. Esta tecnoloxía úsase amplamente na industria debido ao seu baixo custo, alta eficiencia e ampla aplicabilidade.
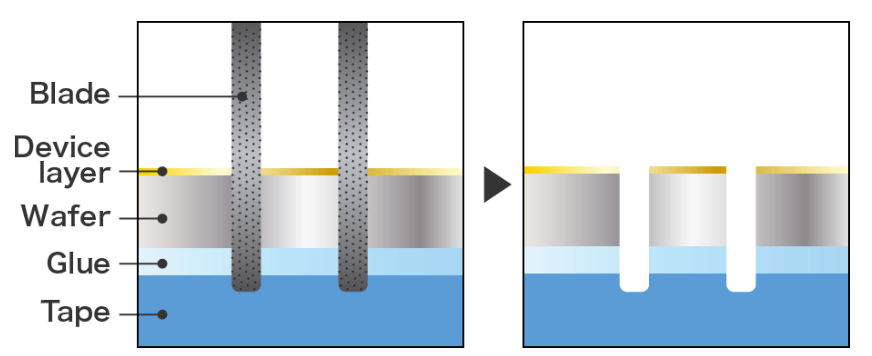
Vantaxes
A alta dureza e resistencia ao desgaste das ferramentas de rectificado de diamante permiten que a tecnoloxía de corte mecánico se adapte ás necesidades de corte de diversos materiais de oblea, xa sexan materiais tradicionais a base de silicio ou semicondutores compostos máis novos. O seu funcionamento é sinxelo, con requisitos técnicos relativamente baixos, o que promove aínda máis a súa popularidade na produción en masa. Ademais, en comparación con outros métodos de corte como o corte por láser, o corte mecánico ten custos máis controlables, o que o fai axeitado para as necesidades de produción de alto volume.
Limitacións
Malia as súas numerosas vantaxes, a tecnoloxía de corte mecánico tamén ten limitacións. En primeiro lugar, debido ao contacto físico entre a ferramenta e a oblea, a precisión do corte é relativamente limitada, o que a miúdo leva a desviacións dimensionais que poden afectar á precisión do empaquetado e as probas posteriores dos chips. En segundo lugar, defectos como lascas e gretas poden producirse facilmente durante o proceso de corte mecánico, o que non só afecta á taxa de rendemento, senón que tamén pode ter un impacto negativo na fiabilidade e na vida útil dos chips. Os danos inducidos pola tensión mecánica son particularmente prexudiciais para a fabricación de chips de alta densidade, especialmente ao cortar materiais fráxiles, onde estes problemas son máis prominentes.
Melloras tecnolóxicas
Para superar estas limitacións, os investigadores optimizan continuamente o proceso de corte mecánico. Entre as melloras clave inclúense a optimización do deseño e a selección de materiais das rebarbas para mellorar a precisión e a durabilidade do corte. Ademais, a optimización do deseño estrutural e dos sistemas de control dos equipos de corte mellorou aínda máis a estabilidade e a automatización do proceso de corte. Estes avances reducen os erros causados polas operacións humanas e melloran a consistencia dos cortes. A introdución de tecnoloxías avanzadas de inspección e control de calidade para a monitorización en tempo real das anomalías durante o proceso de corte tamén mellorou significativamente a fiabilidade e o rendemento do corte.
Desenvolvemento futuro e novas tecnoloxías
Aínda que a tecnoloxía de corte mecánico aínda ocupa unha posición significativa no corte de obleas, as novas tecnoloxías de corte están a avanzar rapidamente a medida que evolucionan os procesos de semicondutores. Por exemplo, a aplicación da tecnoloxía de corte por láser térmico proporciona novas solucións aos problemas de precisión e defectos no corte mecánico. Este método de corte sen contacto reduce a tensión física na oblea, diminuíndo significativamente a incidencia de lascas e gretas, especialmente ao cortar materiais máis fráxiles. No futuro, a integración da tecnoloxía de corte mecánico coas técnicas de corte emerxentes proporcionará á fabricación de semicondutores máis opcións e flexibilidade, mellorando aínda máis a eficiencia da fabricación e a calidade dos chips.
En conclusión, aínda que a tecnoloxía de corte mecánico ten certos inconvenientes, as continuas melloras tecnolóxicas e a súa integración con novas técnicas de corte permiten que aínda desempeñe un papel importante na fabricación de semicondutores e manteña a súa competitividade nos procesos futuros.
2.2 Tecnoloxía de corte por láser
A tecnoloxía de corte por láser, como novo método de corte de obleas, foi gañando gradualmente unha atención xeneralizada na industria dos semicondutores debido á súa alta precisión, á falta de danos por contacto mecánico e ás súas capacidades de corte rápido. Esta tecnoloxía utiliza a alta densidade de enerxía e a capacidade de enfoque dun raio láser para crear unha pequena zona afectada pola calor na superficie do material da oblea. Cando se aplica o raio láser á oblea, a tensión térmica xerada fai que o material se fracture na localización designada, conseguindo un corte preciso.
Vantaxes da tecnoloxía de corte por láser
• Alta precisiónA capacidade de posicionamento preciso do raio láser permite unha precisión de corte de micras ou incluso nanométricas, cumprindo os requisitos da fabricación moderna de circuítos integrados de alta precisión e alta densidade.
• Sen contacto mecánicoO corte por láser evita o contacto físico coa oblea, o que evita problemas comúns no corte mecánico, como as lascas e as gretas, mellorando significativamente a taxa de rendemento e a fiabilidade dos chips.
• Velocidade de corte rápidaA alta velocidade do corte por láser contribúe a unha maior eficiencia da produción, o que o fai especialmente axeitado para escenarios de produción a grande escala e alta velocidade.
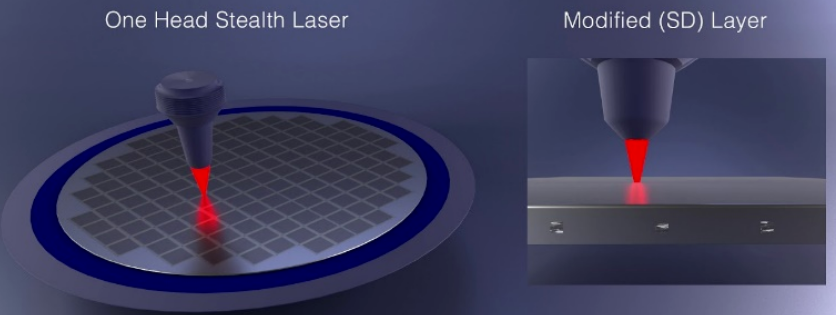
Desafíos afrontados
• Alto custo do equipamentoO investimento inicial en equipos de corte por láser é elevado, o que supón unha presión económica, especialmente para as pequenas e medianas empresas de produción.
• Control de procesos complexosO corte por láser require un control preciso de varios parámetros, como a densidade de enerxía, a posición do foco e a velocidade de corte, o que fai que o proceso sexa complexo.
• Problemas na zona afectada pola calorAínda que a natureza sen contacto do corte por láser reduce os danos mecánicos, a tensión térmica causada pola zona afectada pola calor (HAZ) pode afectar negativamente as propiedades do material da oblea. É necesaria unha maior optimización do proceso para minimizar este efecto.
Direccións de mellora tecnolóxica
Para abordar estes desafíos, os investigadores están a centrarse en reducir os custos dos equipos, mellorar a eficiencia do corte e optimizar o fluxo do proceso.
• Láseres e sistemas ópticos eficientesMediante o desenvolvemento de láseres máis eficientes e sistemas ópticos avanzados, é posible reducir os custos dos equipos e, ao mesmo tempo, mellorar a precisión e a velocidade de corte.
• Optimización dos parámetros do procesoEstanse a levar a cabo investigacións exhaustivas sobre a interacción entre os láseres e os materiais das obleas para mellorar os procesos que reducen a zona afectada pola calor, mellorando así a calidade do corte.
• Sistemas de control intelixentesO desenvolvemento de tecnoloxías de control intelixente ten como obxectivo automatizar e optimizar o proceso de corte por láser, mellorando a súa estabilidade e consistencia.
A tecnoloxía de corte por láser é particularmente eficaz en obleas ultrafinas e en escenarios de corte de alta precisión. A medida que aumentan o tamaño das obleas e as densidades dos circuítos, os métodos tradicionais de corte mecánico teñen dificultades para cumprir as demandas de alta precisión e alta eficiencia da fabricación moderna de semicondutores. Debido ás súas vantaxes únicas, o corte por láser está a converterse na solución preferida nestes campos.
Aínda que a tecnoloxía de corte por láser aínda se enfronta a desafíos como os altos custos dos equipos e a complexidade dos procesos, as súas vantaxes únicas en canto a alta precisión e os danos sen contacto convértena nunha dirección importante para o desenvolvemento na fabricación de semicondutores. A medida que a tecnoloxía láser e os sistemas de control intelixentes continúan avanzando, espérase que o corte por láser mellore aínda máis a eficiencia e a calidade do corte de obleas, impulsando o desenvolvemento continuo da industria dos semicondutores.
2.3 Tecnoloxía de corte por plasma
A tecnoloxía de corte por plasma, como método emerxente de corte en dados de obleas, recibiu unha atención significativa nos últimos anos. Esta tecnoloxía utiliza feixes de plasma de alta enerxía para cortar obleas con precisión controlando a enerxía, a velocidade e a traxectoria de corte do feixe de plasma, conseguindo resultados de corte óptimos.
Principio de funcionamento e vantaxes
O proceso de corte por plasma baséase nun feixe de plasma de alta temperatura e alta enerxía xerado polo equipo. Este feixe pode quentar o material da oblea ata o seu punto de fusión ou vaporización nun período de tempo moi curto, o que permite un corte rápido. En comparación co corte mecánico ou láser tradicional, o corte por plasma é máis rápido e produce unha zona afectada pola calor máis pequena, o que reduce eficazmente a aparición de gretas e danos durante o corte.
En aplicacións prácticas, a tecnoloxía de corte por plasma é particularmente hábil para manexar obleas con formas complexas. O seu feixe de plasma axustable e de alta enerxía pode cortar facilmente obleas de formas irregulares con alta precisión. Polo tanto, na fabricación de microelectrónica, especialmente na produción personalizada e en lotes pequenos de chips de alta gama, esta tecnoloxía é moi prometedora para un uso xeneralizado.
Desafíos e limitacións
A pesar das moitas vantaxes da tecnoloxía de corte por plasma, tamén se enfronta a algúns desafíos.
• Proceso complexoO proceso de corte por plasma é complexo e require equipos de alta precisión e operadores experimentados para garantirprecisión e estabilidade no corte.
• Control ambiental e seguridadeA natureza de alta temperatura e alta enerxía do feixe de plasma require rigorosas medidas de control ambiental e seguridade, o que aumenta a complexidade e o custo da implementación.
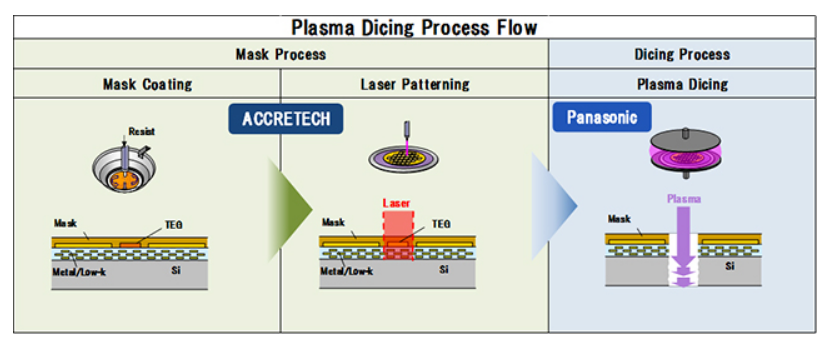
Direccións de desenvolvemento futuro
Cos avances tecnolóxicos, espérase que os desafíos asociados ao corte por plasma se superen gradualmente. Ao desenvolver equipos de corte máis intelixentes e estables, pódese reducir a dependencia das operacións manuais, mellorando así a eficiencia da produción. Ao mesmo tempo, a optimización dos parámetros do proceso e do ambiente de corte axudará a reducir os riscos de seguridade e os custos operativos.
Na industria dos semicondutores, as innovacións na tecnoloxía de corte e tronzado de obleas son cruciais para impulsar o desenvolvemento da industria. A tecnoloxía de corte por plasma, coa súa alta precisión, eficiencia e capacidade para manexar formas complexas de obleas, xurdiu como un novo actor importante neste campo. Aínda que persisten algúns desafíos, estes problemas abordaranse gradualmente coa innovación tecnolóxica continua, o que traerá máis posibilidades e oportunidades á fabricación de semicondutores.
As perspectivas de aplicación da tecnoloxía de corte por plasma son amplas e espérase que desempeñe un papel máis importante na fabricación de semicondutores no futuro. Mediante a innovación e optimización tecnolóxicas continuas, o corte por plasma non só abordará os desafíos existentes, senón que tamén se converterá nun poderoso motor do crecemento da industria dos semicondutores.
2.4 Calidade de corte e factores que inflúen
A calidade do corte das obleas é fundamental para o posterior empaquetado dos chips, as probas e o rendemento e a fiabilidade xerais do produto final. Entre os problemas habituais que se atopan durante o corte inclúense fendas, lascas e desviacións no corte. Estes problemas están influenciados por varios factores que actúan conxuntamente.
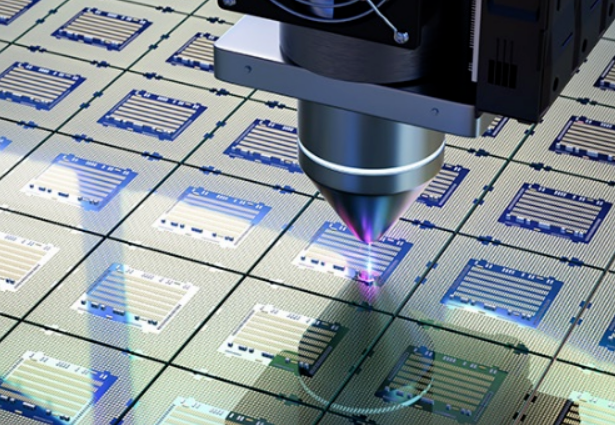
Categoría | Contido | Impacto |
Parámetros do proceso | A velocidade de corte, a velocidade de avance e a profundidade de corte afectan directamente á estabilidade e á precisión do proceso de corte. Uns axustes incorrectos poden levar a unha concentración de tensión e a unha zona afectada pola calor excesiva, o que resulta en gretas e lascas. Axustar os parámetros axeitadamente en función do material da oblea, o grosor e os requisitos de corte é fundamental para acadar os resultados de corte desexados. | Os parámetros de proceso axeitados garanten un corte preciso e reducen o risco de defectos como gretas e lascas. |
Factores de equipamento e materiais | -Calidade da láminaO material, a dureza e a resistencia ao desgaste da lámina inflúen na suavidade do proceso de corte e na planitude da superficie de corte. As láminas de mala calidade aumentan a fricción e a tensión térmica, o que pode provocar gretas ou lascas. Escoller o material axeitado da lámina é crucial. -Rendemento do refrixeranteOs refrixerantes axudan a reducir a temperatura de corte, minimizar a fricción e eliminar os residuos. Un refrixerante ineficaz pode provocar altas temperaturas e acumulación de residuos, o que afecta á calidade e á eficiencia do corte. Seleccionar refrixerantes eficientes e respectuosos co medio ambiente é vital. | A calidade da folla afecta á precisión e á suavidade do corte. Un refrixerante ineficaz pode resultar nunha mala calidade e eficiencia de corte, o que pon de manifesto a necesidade dun uso óptimo do refrixerante. |
Control de procesos e inspección de calidade | -Control de procesosMonitorización e axuste en tempo real dos parámetros clave de corte para garantir a estabilidade e a consistencia no proceso de corte. -Inspección de calidadeAs comprobacións de aspecto posteriores ao corte, as medicións dimensionais e as probas de rendemento eléctrico axudan a identificar e abordar os problemas de calidade con prontitude, mellorando a precisión e a consistencia do corte. | Un control de procesos e unha inspección de calidade axeitados axudan a garantir resultados de corte consistentes e de alta calidade, así como a detección temperá de posibles problemas. |

Mellora da calidade de corte
Mellorar a calidade do corte require unha abordaxe integral que teña en conta os parámetros do proceso, a selección de equipos e materiais, o control e a inspección do proceso. Ao refinar continuamente as tecnoloxías de corte e optimizar os métodos de proceso, pódese mellorar aínda máis a precisión e a estabilidade do corte de obleas, proporcionando un soporte técnico máis fiable para a industria de fabricación de semicondutores.
#03 Manipulación e probas posteriores ao corte
3.1 Limpeza e secado
Os pasos de limpeza e secado despois do corte da oblea son fundamentais para garantir a calidade do chip e a progresión sen problemas dos procesos posteriores. Durante esta etapa, é esencial eliminar completamente os restos de silicio, os residuos de refrixerante e outros contaminantes xerados durante o corte. É igualmente importante garantir que os chips non se danen durante o proceso de limpeza e, despois do secado, garantir que non quede humidade na superficie do chip para evitar problemas como a corrosión ou a descarga electrostática.
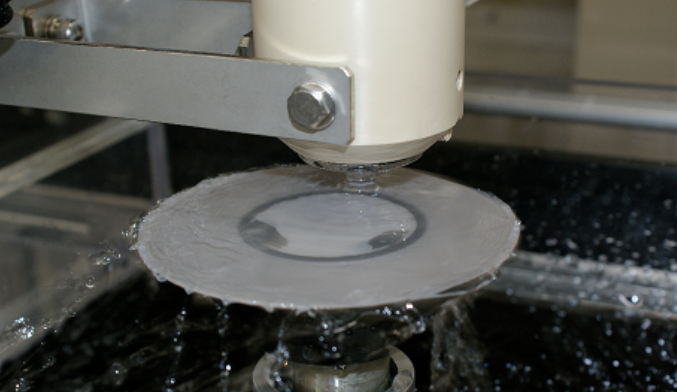
Manexo posterior ao corte: proceso de limpeza e secado
Paso do proceso | Contido | Impacto |
Proceso de limpeza | -MétodoEmpregar produtos de limpeza especializados e auga pura, combinados con técnicas de cepillado ultrasónico ou mecánico para a limpeza. | Garante a eliminación completa de contaminantes e evita danos nas lascas durante a limpeza. |
-Selección de axente de limpezaEscolla en función do material da oblea e do tipo de contaminante para garantir unha limpeza eficaz sen danar o chip. | A selección axeitada do axente é fundamental para unha limpeza eficaz e unha protección contra as lascas. | |
-Control de parámetrosControle estritamente a temperatura, o tempo e a concentración da solución de limpeza para evitar problemas de calidade causados por unha limpeza inadecuada. | Os controis axudan a evitar danar a oblea ou deixar contaminantes, garantindo unha calidade consistente. | |
Proceso de secado | -Métodos tradicionaisSecado ao aire natural e secado ao aire quente, que teñen baixa eficiencia e poden provocar acumulación de electricidade estática. | Pode provocar tempos de secado máis lentos e posibles problemas de electricidade estática. |
-Tecnoloxías modernasEmpregar tecnoloxías avanzadas como o secado ao baleiro e o secado por infravermellos para garantir que as lascas sequen rapidamente e evitar efectos nocivos. | Proceso de secado máis rápido e eficiente, que reduce o risco de descarga estática ou problemas relacionados coa humidade. | |
Selección e mantemento de equipos | -Selección de equiposAs máquinas de limpeza e secado de alto rendemento melloran a eficiencia do procesamento e controlan con precisión os posibles problemas durante a manipulación. | As máquinas de alta calidade garanten un mellor procesamento e reducen a probabilidade de erros durante a limpeza e o secado. |
-Mantemento de equiposA inspección e o mantemento regulares dos equipos garanten que se manteñan en condicións de funcionamento óptimas, garantindo a calidade das lascas. | Un mantemento axeitado evita avarías nos equipos, garantindo un procesamento fiable e de alta calidade. |
Limpeza e secado posteriores ao corte
As etapas de limpeza e secado despois do corte das obleas son procesos complexos e delicados que requiren unha coidadosa consideración de múltiples factores para garantir o resultado final do procesamento. Mediante o uso de métodos científicos e procedementos rigorosos, é posible garantir que cada chip entre nas etapas posteriores de empaquetado e probas en condicións óptimas.
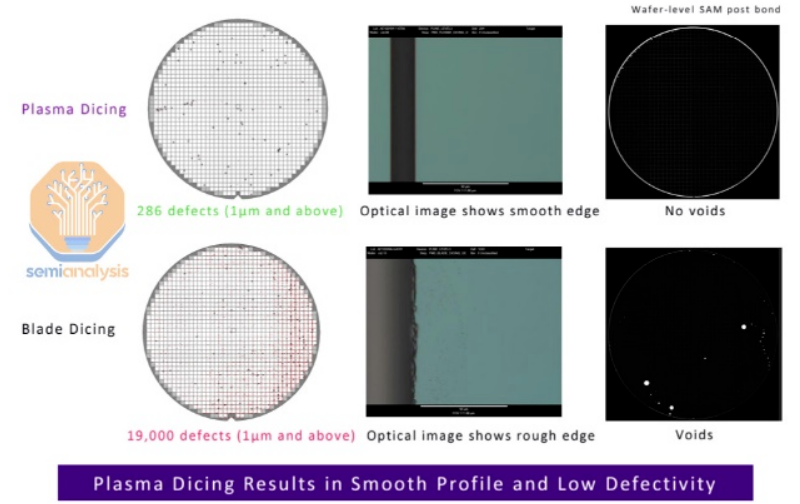
Inspección e probas posteriores ao corte
Paso | Contido | Impacto |
Paso de inspección | 1.Inspección visualEmpregar equipos de inspección visual ou automatizados para comprobar se hai defectos visibles como gretas, lascas ou contaminación na superficie da lasca. Identificar rapidamente as lascas danadas fisicamente para evitar desperdicios. | Axuda a identificar e eliminar as lascas defectuosas no inicio do proceso, o que reduce a perda de material. |
2.Medición de tamañoEmpregar dispositivos de medición de precisión para medir con precisión as dimensións dos chips, garantindo que o tamaño do corte cumpra as especificacións de deseño e evitando problemas de rendemento ou dificultades de empaquetado. | Garante que os chips estean dentro dos límites de tamaño requiridos, evitando a degradación do rendemento ou problemas de montaxe. | |
3.Probas de rendemento eléctricoAvaliar parámetros eléctricos clave, como a resistencia, a capacitancia e a inductancia, para identificar os chips non conformes e garantir que só os chips con bo rendemento pasen á seguinte fase. | Garante que só os chips funcionais e de rendemento probado avancen no proceso, o que reduce o risco de fallo en etapas posteriores. | |
Paso de proba | 1.Probas funcionaisVerificar que a funcionalidade básica do chip funcione segundo o previsto, identificando e eliminando os chips con anomalías funcionais. | Garante que os chips cumpran os requisitos operativos básicos antes de pasar a etapas posteriores. |
2.Probas de fiabilidadeAvaliar a estabilidade do rendemento do chip en condicións de uso prolongado ou en ambientes agresivos, o que normalmente implica o envellecemento a altas temperaturas, probas a baixas temperaturas e probas de humidade para simular condicións extremas do mundo real. | Garante que os chips poidan funcionar de forma fiable nunha ampla gama de condicións ambientais, mellorando a lonxevidade e a estabilidade do produto. | |
3.Probas de compatibilidadeVerificar que o chip funcione correctamente con outros compoñentes ou sistemas, garantindo que non haxa fallos nin degradación do rendemento debido á incompatibilidade. | Garante un funcionamento sen problemas en aplicacións do mundo real evitando problemas de compatibilidade. |
3.3 Embalaxe e almacenamento
Despois do corte das obleas, os chips son un resultado crucial do proceso de fabricación de semicondutores, e as súas etapas de empaquetado e almacenamento son igualmente importantes. As medidas axeitadas de empaquetado e almacenamento son esenciais non só para garantir a seguridade e a estabilidade dos chips durante o transporte e o almacenamento, senón tamén para proporcionar un soporte sólido para as etapas posteriores de produción, probas e empaquetado.
Resumo das etapas de inspección e probas:
Os pasos de inspección e probas dos chips despois do corte da oblea abarcan unha serie de aspectos, incluíndo a inspección visual, a medición do tamaño, as probas de rendemento eléctrico, as probas funcionais, as probas de fiabilidade e as probas de compatibilidade. Estes pasos están interconectados e complementarios, formando unha barreira sólida para garantir a calidade e a fiabilidade do produto. Mediante procedementos rigorosos de inspección e probas, pódense identificar e resolver posibles problemas con prontitude, garantindo que o produto final cumpra os requisitos e as expectativas do cliente.
Aspecto | Contido |
Medidas de embalaxe | 1.AntiestáticoOs materiais de embalaxe deben ter excelentes propiedades antiestáticas para evitar que a electricidade estática dane os dispositivos ou afecte ao seu rendemento. |
2.Resistente á humidadeOs materiais de embalaxe deben ter unha boa resistencia á humidade para evitar a corrosión e o deterioro do rendemento eléctrico causado pola humidade. | |
3.Resistente aos golpesOs materiais de embalaxe deben proporcionar unha absorción eficaz dos impactos para protexer as lascas das vibracións e os impactos durante o transporte. | |
Ambiente de almacenamento | 1.Control da humidadeControle estritamente a humidade dentro dun rango axeitado para evitar a absorción de humidade e a corrosión causadas polo exceso de humidade ou problemas estáticos causados pola baixa humidade. |
2.LimpezaManteña un ambiente de almacenamento limpo para evitar a contaminación das lascas por po e impurezas. | |
3.Control de temperatura: Estableza un rango de temperatura razoable e manteña a estabilidade da temperatura para evitar o envellecemento acelerado debido á calor excesiva ou problemas de condensación causados polas baixas temperaturas. | |
Inspección regular | Inspeccione e avalíe regularmente as fichas almacenadas, mediante inspeccións visuais, medicións de tamaño e probas de rendemento eléctrico para identificar e abordar posibles problemas de maneira oportuna. En función do tempo e as condicións de almacenamento, planifique o uso das fichas para garantir que se utilicen en condicións óptimas. |
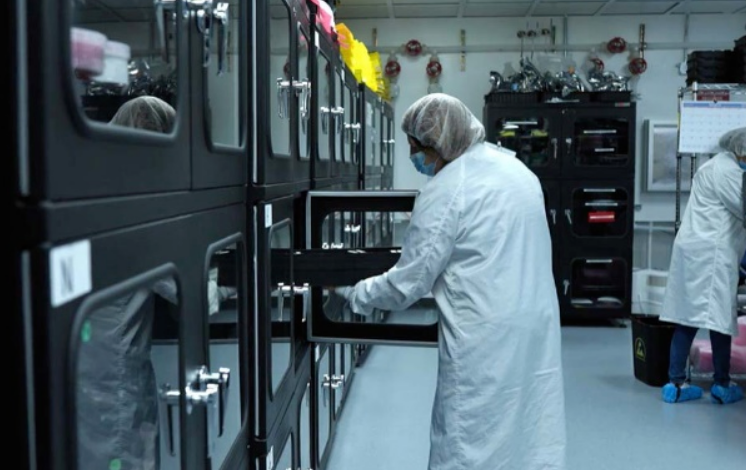
O problema das microfendas e danos durante o proceso de corte en dados das obleas é un desafío importante na fabricación de semicondutores. A tensión de corte é a principal causa deste fenómeno, xa que crea pequenas fendas e danos na superficie da oblea, o que leva a un aumento dos custos de fabricación e a unha diminución da calidade do produto.
Para abordar este desafío, é crucial minimizar a tensión de corte e implementar técnicas, ferramentas e condicións de corte optimizadas. Unha atención coidadosa a factores como o material da lámina, a velocidade de corte, a presión e os métodos de arrefriamento pode axudar a reducir a formación de microfendas e mellorar o rendemento xeral do proceso. Ademais, a investigación en curso sobre tecnoloxías de corte máis avanzadas, como o corte por láser, está a explorar formas de mitigar aínda máis estes problemas.
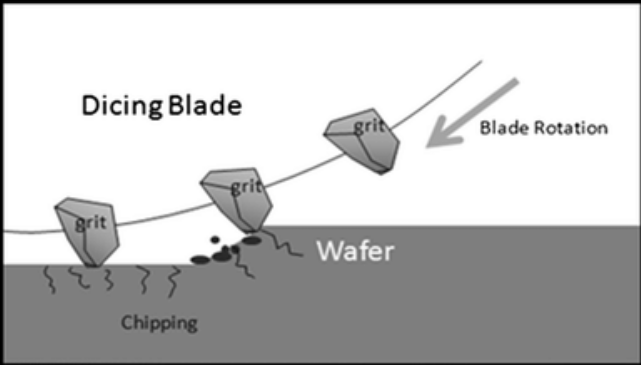
Como material fráxil, as obleas son propensas a cambios estruturais internos cando se someten a tensións mecánicas, térmicas ou químicas, o que leva á formación de microfendas. Aínda que estas fendas poden non ser inmediatamente perceptibles, poden expandirse e causar danos máis graves a medida que avanza o proceso de fabricación. Este problema vólvese especialmente problemático durante as etapas posteriores de empaquetado e probas, onde as flutuacións de temperatura e as tensións mecánicas adicionais poden facer que estas microfendas evolucionen cara a fracturas visibles, o que pode levar á falla do chip.
Para mitigar este risco, é esencial controlar o proceso de corte coidadosamente optimizando parámetros como a velocidade de corte, a presión e a temperatura. O uso de métodos de corte menos agresivos, como o corte por láser, pode reducir a tensión mecánica na oblea e minimizar a formación de microfendas. Ademais, a implementación de métodos de inspección avanzados como a dixitalización por infravermellos ou a imaxe de raios X durante o proceso de corte da oblea pode axudar a detectar estas fendas en fase inicial antes de que causen máis danos.
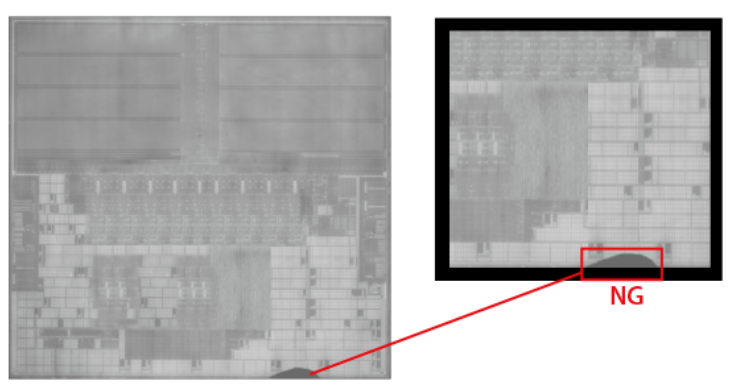
Os danos na superficie da oblea son unha preocupación importante no proceso de corte en dados, xa que poden ter un impacto directo no rendemento e a fiabilidade do chip. Estes danos poden ser causados polo uso inadecuado de ferramentas de corte, parámetros de corte incorrectos ou defectos de material inherentes á propia oblea. Independentemente da causa, estes danos poden levar a alteracións na resistencia eléctrica ou na capacitancia do circuíto, o que afecta ao rendemento xeral.
Para abordar estes problemas, están a explorarse dúas estratexias principais:
1. Optimización de ferramentas e parámetros de corteAo usar láminas máis afiadas, axustar a velocidade de corte e modificar a profundidade de corte, pódese minimizar a concentración de tensión durante o proceso de corte, reducindo así o potencial de danos.
2. Explorando novas tecnoloxías de corteAs técnicas avanzadas como o corte por láser e o corte por plasma ofrecen unha maior precisión e, ao mesmo tempo, reducen potencialmente o nivel de dano inflixido á oblea. Estas tecnoloxías están a ser estudadas para atopar xeitos de conseguir unha alta precisión de corte e minimizar a tensión térmica e mecánica na oblea.
Área de impacto térmico e os seus efectos no rendemento
Nos procesos de corte térmico, como o corte por láser e plasma, as altas temperaturas crean inevitablemente unha zona de impacto térmico na superficie da oblea. Esta área, onde o gradiente de temperatura é significativo, pode alterar as propiedades do material, afectando o rendemento final do chip.
Impacto da Zona Afectada Térmicamente (TAZ):
Cambios na estrutura cristalinaA altas temperaturas, os átomos do material da oblea poden reorganizarse, causando distorsións na estrutura cristalina. Esta distorsión debilita o material, reducindo a súa resistencia mecánica e estabilidade, o que aumenta o risco de fallo do chip durante o seu uso.
Cambios nas propiedades eléctricasAs altas temperaturas poden alterar a concentración e a mobilidade dos portadores nos materiais semicondutores, o que afecta á condutividade eléctrica e á eficiencia da transmisión de corrente do chip. Estes cambios poden provocar unha diminución do rendemento do chip, o que podería facelo inadecuado para o seu propósito previsto.
Para mitigar estes efectos, controlar a temperatura durante o corte, optimizar os parámetros de corte e explorar métodos como os chorros de arrefriamento ou os tratamentos de posprocesamento son estratexias esenciais para reducir a extensión do impacto térmico e manter a integridade do material.
En xeral, tanto as microfendas como as zonas de impacto térmico son desafíos cruciais na tecnoloxía de corte en dados de obleas. Será necesaria unha investigación continua, xunto cos avances tecnolóxicos e as medidas de control de calidade, para mellorar a calidade dos produtos semicondutores e aumentar a súa competitividade no mercado.
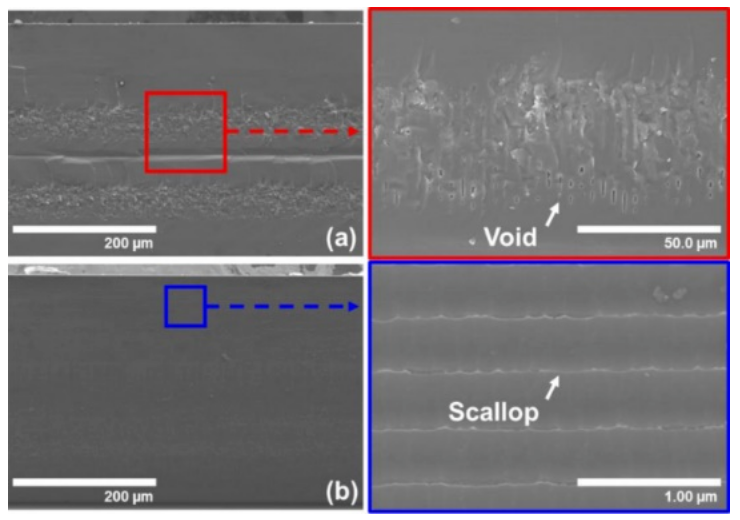
Medidas para controlar a zona de impacto térmico:
Optimización dos parámetros do proceso de corteReducir a velocidade e a potencia de corte pode minimizar eficazmente o tamaño da zona de impacto térmico (TAZ). Isto axuda a controlar a cantidade de calor xerada durante o proceso de corte, o que afecta directamente ás propiedades do material da oblea.
Tecnoloxías avanzadas de refrixeraciónA aplicación de tecnoloxías como o arrefriamento con nitróxeno líquido e o arrefriamento microfluídico pode limitar significativamente o alcance da zona de impacto térmico. Estes métodos de arrefriamento axudan a disipar a calor de forma máis eficiente, preservando así as propiedades do material da oblea e minimizando os danos térmicos.
Selección de materiaisOs investigadores están a explorar novos materiais, como os nanotubos de carbono e o grafeno, que posúen unha excelente condutividade térmica e resistencia mecánica. Estes materiais poden reducir a zona de impacto térmico e mellorar o rendemento xeral dos chips.
En resumo, aínda que a zona de impacto térmico é unha consecuencia inevitable das tecnoloxías de corte térmico, pódese controlar eficazmente mediante técnicas de procesamento optimizadas e selección de materiais. É probable que a investigación futura se centre no axuste fino e a automatización dos procesos de corte térmico para lograr un corte en dados de obleas máis eficiente e preciso.

Estratexia de equilibrio:
Conseguir o equilibrio óptimo entre o rendemento das obleas e a eficiencia da produción é un desafío continuo na tecnoloxía de corte de obleas. Os fabricantes deben ter en conta múltiples factores, como a demanda do mercado, os custos de produción e a calidade do produto, para desenvolver unha estratexia de produción e uns parámetros de proceso racionais. Ao mesmo tempo, a introdución de equipos de corte avanzados, a mellora das habilidades dos operadores e a mellora do control da calidade das materias primas son esenciais para manter ou mesmo mellorar o rendemento e, ao mesmo tempo, aumentar a eficiencia da produción.
Desafíos e oportunidades futuras:
Co avance da tecnoloxía dos semicondutores, o corte de obleas enfróntase a novos desafíos e oportunidades. A medida que o tamaño dos chips se reduce e a integración aumenta, as esixencias de precisión e calidade de corte medran significativamente. Simultaneamente, as tecnoloxías emerxentes proporcionan novas ideas para o desenvolvemento de técnicas de corte de obleas. Os fabricantes deben estar atentos á dinámica do mercado e ás tendencias tecnolóxicas, axustando e optimizando continuamente as estratexias de produción e os parámetros do proceso para satisfacer os cambios do mercado e as demandas tecnolóxicas.
En conclusión, ao integrar as consideracións da demanda do mercado, os custos de produción e a calidade do produto, e ao introducir equipos e tecnoloxía avanzados, mellorar as habilidades dos operadores e reforzar o control das materias primas, os fabricantes poden lograr o mellor equilibrio entre o rendemento das obleas e a eficiencia da produción durante o corte en dados das obleas, o que leva a unha produción eficiente e de alta calidade de produtos semicondutores.
Perspectivas futuras:
Cos rápidos avances tecnolóxicos, a tecnoloxía dos semicondutores está a progresar a un ritmo sen precedentes. Como paso fundamental na fabricación de semicondutores, a tecnoloxía de corte de obleas está preparada para novos e emocionantes desenvolvementos. De cara ao futuro, espérase que a tecnoloxía de corte de obleas logre melloras significativas en precisión, eficiencia e custo, inxectando nova vitalidade ao crecemento continuo da industria dos semicondutores.
Aumento da precisión:
Na procura dunha maior precisión, a tecnoloxía de corte de obleas levará continuamente ao límite dos procesos existentes. Ao estudar en profundidade os mecanismos físicos e químicos do proceso de corte e controlar con precisión os parámetros de corte, conseguiranse resultados de corte máis finos para cumprir cos requisitos de deseño de circuítos cada vez máis complexos. Ademais, a exploración de novos materiais e métodos de corte mellorará significativamente o rendemento e a calidade.
Mellora da eficiencia:
Os novos equipos de corte de obleas centraranse no deseño intelixente e automatizado. A introdución de sistemas de control e algoritmos avanzados permitirá que os equipos axusten automaticamente os parámetros de corte para adaptarse a diferentes materiais e requisitos de deseño, mellorando así significativamente a eficiencia da produción. As innovacións como a tecnoloxía de corte de varias obleas e os sistemas de substitución rápida de láminas xogarán un papel crucial na mellora da eficiencia.
Redución de custos:
A redución de custos é unha dirección clave para o desenvolvemento da tecnoloxía de corte de obleas. A medida que se desenvolven novos materiais e métodos de corte, espérase que os custos dos equipos e os gastos de mantemento se controlen de forma eficaz. Ademais, a optimización dos procesos de produción e a redución das taxas de refugallo reducirán aínda máis os residuos durante a fabricación, o que levará a unha diminución dos custos de produción globais.
Fabricación intelixente e IoT:
A integración da fabricación intelixente e as tecnoloxías da Internet das Cousas (IoT) traerá cambios transformadores á tecnoloxía de corte de obleas. Mediante a interconectividade e o intercambio de datos entre dispositivos, cada paso do proceso de produción pode ser monitorizado e optimizado en tempo real. Isto non só mellora a eficiencia da produción e a calidade do produto, senón que tamén proporciona ás empresas unha previsión de mercado e un apoio na toma de decisións máis precisos.
No futuro, a tecnoloxía de corte de obleas fará avances notables en precisión, eficiencia e custo. Estes avances impulsarán o desenvolvemento continuo da industria dos semicondutores e traerán máis innovacións tecnolóxicas e comodidades á sociedade humana.
Data de publicación: 19 de novembro de 2024