Forno de crecemento de cristal de SiC de 4 polgadas, 6 polgadas e 8 polgadas para o proceso CVD
Principio de funcionamento
O principio fundamental do noso sistema de deposición química en fase CVD implica a descomposición térmica de gases precursores que conteñen silicio (por exemplo, SiH4) e carbono (por exemplo, C3H8) a altas temperaturas (normalmente 1500-2000 °C), depositando monocristais de SiC sobre substratos mediante reaccións químicas en fase gasosa. Esta tecnoloxía é especialmente axeitada para producir monocristais de 4H/6H-SiC de alta pureza (>99,9995 %) con baixa densidade de defectos (<1000/cm²), cumprindo os estritos requisitos de materiais para electrónica de potencia e dispositivos de radiofrecuencia. Mediante un control preciso da composición do gas, o caudal e o gradiente de temperatura, o sistema permite unha regulación precisa do tipo de condutividade do cristal (tipo N/P) e da resistividade.
Tipos de sistemas e parámetros técnicos
Tipo de sistema | Rango de temperatura | Características principais | Aplicacións |
CVD de alta temperatura | 1500-2300 °C | Quecemento por indución de grafito, uniformidade de temperatura de ±5 °C | Crecemento de cristais de SiC a granel |
CVD con filamentos quentes | 800-1400 °C | Quecemento de filamentos de tungsteno, taxa de deposición de 10-50 μm/h | Epitaxia espesa de SiC |
VPE CVD | 1200-1800 °C | Control de temperatura multizona, utilización de gas >80 % | Produción masiva de epi-obleas |
PECVD | 400-800 °C | Plasma mellorado, taxa de deposición de 1-10 μm/h | Películas delgadas de SiC de baixa temperatura |
Características técnicas principais
1. Sistema avanzado de control de temperatura
O forno conta cun sistema de quecemento resistivo multizona capaz de manter temperaturas de ata 2300 °C cunha uniformidade de ±1 °C en toda a cámara de crecemento. Esta xestión térmica de precisión conséguese mediante:
12 zonas de calefacción controladas independentemente.
Monitorización redundante de termopar (Tipo C W-Re).
Algoritmos de axuste de perfís térmicos en tempo real.
Paredes da cámara refrixeradas por auga para o control do gradiente térmico.
2. Tecnoloxía de subministración e mestura de gases
O noso sistema patentado de distribución de gas garante unha mestura óptima de precursores e unha subministración uniforme:
Controladores de caudal másico con precisión de ±0,05 sccm.
Colector de inxección de gas multipunto.
Monitorización in situ da composición de gases (espectroscopia FTIR).
Compensación automática do fluxo durante os ciclos de crecemento.
3. Mellora da calidade cristalina
O sistema incorpora varias innovacións para mellorar a calidade dos cristais:
Soporte de substrato rotatorio (programable de 0 a 100 rpm).
Tecnoloxía avanzada de control da capa límite.
Sistema de monitorización de defectos in situ (dispersión láser UV).
Compensación automática do estrés durante o crecemento.
4. Automatización e control de procesos
Execución de receitas totalmente automatizada.
Optimización de parámetros de crecemento en tempo real mediante IA.
Monitorización e diagnóstico remotos.
Rexistro de datos de máis de 1000 parámetros (almacenados durante 5 anos).
5. Características de seguridade e fiabilidade
Protección contra sobretemperatura con tripla redundanza.
Sistema automático de purga de emerxencia.
Deseño estrutural con clasificación sísmica.
Garantía de funcionamento do 98,5 %.
6. Arquitectura escalable
O deseño modular permite melloras na capacidade.
Compatible con tamaños de oblea de 100 mm a 200 mm.
Admite configuracións verticais e horizontais.
Compoñentes de cambio rápido para mantemento.
7. Eficiencia enerxética
Consumo de enerxía un 30 % menor que outros sistemas comparables.
O sistema de recuperación de calor captura o 60 % da calor residual.
Algoritmos de consumo de gas optimizados.
Requisitos das instalacións que cumpren coa normativa LEED.
8. Versatilidade do material
Cultiva todos os principais politipos de SiC (4H, 6H, 3C).
Admite variantes condutivas e semiillantes.
Admite varios esquemas de dopaxe (tipo N, tipo P).
Compatible con precursores alternativos (por exemplo, TMS, TES).
9. Rendemento do sistema de baleiro
Presión base: <1×10⁻⁶ Torr
Taxa de fuga: <1×10⁻⁹ Torr·L/seg
Velocidade de bombeo: 5000 L/s (para SiH₄)
Control automático da presión durante os ciclos de crecemento
Esta exhaustiva especificación técnica demostra a capacidade do noso sistema para producir cristais de SiC de calidade de investigación e produción con consistencia e rendemento líderes na industria. A combinación de control de precisión, monitorización avanzada e enxeñaría robusta fai deste sistema CVD a opción óptima tanto para aplicacións de I+D como de fabricación en volume en electrónica de potencia, dispositivos de RF e outras aplicacións avanzadas de semicondutores.
Vantaxes principais
1. Crecemento de cristais de alta calidade
• Densidade de defectos tan baixa como <1000/cm² (4H-SiC)
• Uniformidade de dopaxe <5 % (obleas de 6 polgadas)
• Pureza cristalina >99,9995 %
2. Capacidade de produción de gran tamaño
• Admite o crecemento de obleas de ata 8 polgadas
• Uniformidade do diámetro >99%
• Variación do grosor <±2%
3. Control preciso do proceso
• Precisión do control de temperatura ±1 °C
• Precisión do control do fluxo de gas ±0,1 sccm
• Precisión do control de presión ±0,1 Torr
4. Eficiencia enerxética
• Un 30 % máis eficiente enerxeticamente que os métodos convencionais
• Taxa de crecemento de ata 50-200 μm/h
• Tempo de funcionamento do equipo >95 %
Aplicacións clave
1. Dispositivos electrónicos de potencia
Substratos 4H-SiC de 6 polgadas para MOSFET/díodos de máis de 1200 V, o que reduce as perdas de conmutación nun 50 %.
2. Comunicación 5G
Substratos semiillantes de SiC (resistividade >10⁸Ω·cm) para PA de estacións base, con perda de inserción <0,3dB a >10GHz.
3. Vehículos de novas enerxías
Os módulos de potencia de SiC de calidade automotriz amplían a autonomía dos vehículos eléctricos entre un 5 e un 8 % e reducen o tempo de carga nun 30 %.
4. Inversores fotovoltaicos
Os substratos con baixos defectos aumentan a eficiencia de conversión máis alá do 99 %, á vez que reducen o tamaño do sistema nun 40 %.
Servizos de XKH
1. Servizos de personalización
Sistemas CVD personalizados de 4 a 8 polgadas.
Admite o crecemento de tipos 4H/6H-N, illantes 4H/6H-SEMI, etc.
2. Soporte técnico
Formación integral en optimización de procesos e operacións.
Resposta técnica 24 horas ao día, 7 días á semana.
3. Solucións chave en man
Servizos completos dende a instalación ata a validación do proceso.
4. Suministro de materiais
Substratos/obleas epi de SiC de 2 a 12 polgadas dispoñibles.
Admite politipos 4H/6H/3C.
Os diferenciadores clave inclúen:
Capacidade de crecemento de cristais de ata 8 polgadas.
Un 20 % máis rápido que a media do sector.
98 % de fiabilidade do sistema.
Paquete completo de sistemas de control intelixente.
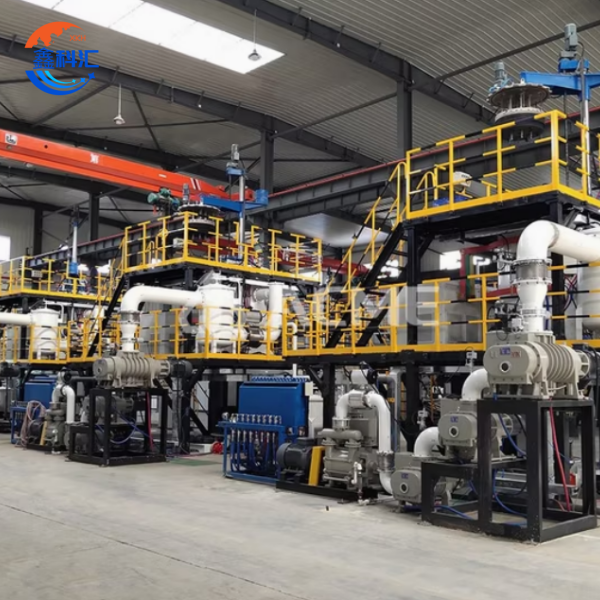
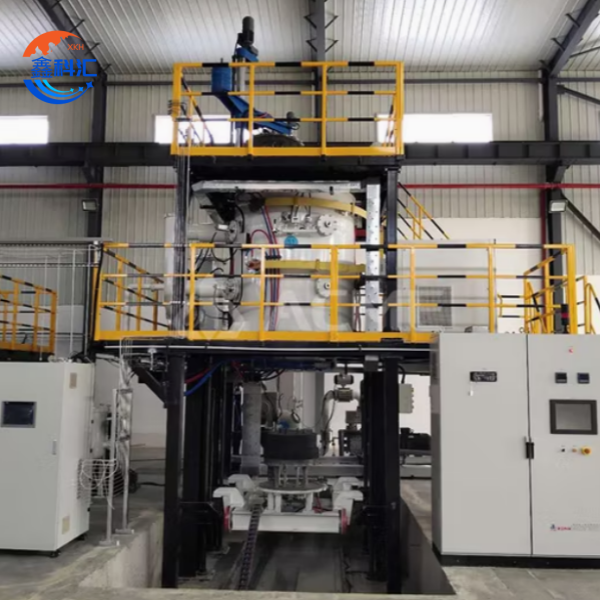